products used: Soy Gel paint stripper, trisodium phosphate, Rapid Refloor polyurethane/polyurea, Sikagard 62 epoxy coating
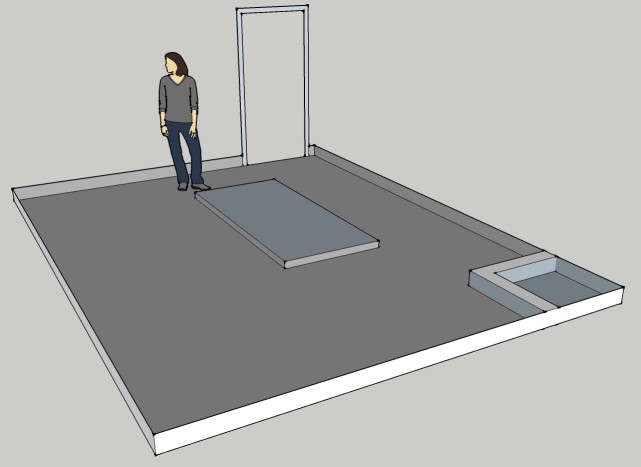
PROJECT DESCRIPTION:
Occasionally water is discharged onto the floor in a mechanical room near a loading dock. When that happens areas adjacent to and under the room get a little wet. The building engineer asked what we could do about it. The solution was to line the floor and bottom of the walls with an epoxy coating so that the water would be contained until maintenance personnel could collect it. The work took two days.
PROCEDURE:
First the surface had to be prepared. Prep work is important and often the hardest part of the job. This time the old paint was removed with Soy Gel paint stripper. We didn’t know what was put on the concrete floor before so we tested several different strippers and the Soy Gel worked best. The floor area was 241 square feet. About 2 1/2 gallons of stripper was spread over the floor and allowed to dwell for an hour-and-a-half. Because the concrete had a broom finish the stripper and paint residue had to be scraped and brushed out of the brush marks in the concrete. After all that could be lifted with scrapers, putty knives and wire brushes was disposed of, the surface was flushed with water and then a solution of trisodium phosphate. The slurry became mud and hard to lift but we were able to get it up with more brushing and a wet-dry vac. The Soy Gel continued to act on the paint while we worked with wire brushes so as time passed less mechanical action was needed. It probably would have been better to let the stripper dwell twice as long before trying to get it up. Also, another Soy Gel product, “Emerge Degreaser”, could have been used to make clean-up easier.
The next day the floor was dry. Removing what was left was done with sweeping and a vacuum.
Cracks totaling about twenty feet in length were ground and filled with “Rapid Refloor” polyurethane/polyurea which cured in about fifteen minutes. Two coats of Sikagard 62 epoxy coating were then applied. Sikagard 62 is primarily used as a protective coating or lining for secondary containment structures. Another use is seamless flooring. This application was both. The AIA division 9 specification Sika offers on using the material for seamless flooring calls for a primer coat, a binder coat covered with sand and a finish coat. All that wasn’t necessary for this job so we applied the material according to the procedure for protective coatings.
The first coat coverage was 126 square feet per gallon. So two gallons was barely enough to finish the first coat. Once the A and B components are mixed the material starts to cure and it’s pot life is only about forty minutes so if there isn’t extra material you have to be careful. There were just three of us so we mixed one gallon and divided it between us. That turned out well because it took almost 40 minutes to spread what we mixed.
Using rollers made for epoxy/adhesive is better than rollers made for paint or another material.
We waited until we could walk on the floor which took a couple hours and then applied the second coat. The second coat went on more quickly with a coverage rate of about 167 square feet per gallon which is in the range that Sika says you should get. (There was about two quarts left when we finished.)
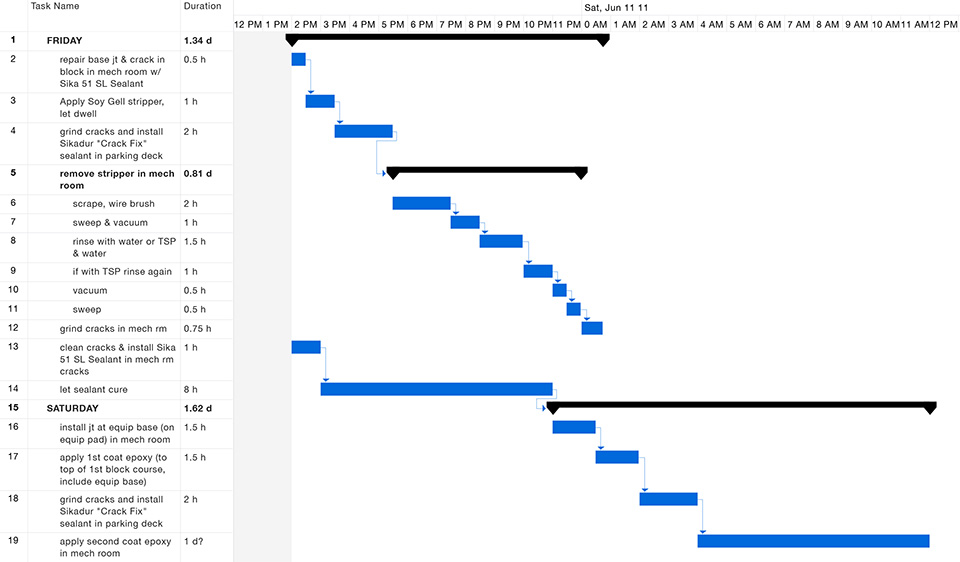
The job had to be completed over a weekend. The detailed production schedule helped to ensure that requirement was met. Use of project management software permits assignment of tools, materials, personnel and other “resources” to tasks, which helps ensure that everything needed for the job is in place.